SAGE
Thermal Battery
Thermal battery is a disposable electrochemical power source that is widely used as the main power source in guidance kits, fuzes, missiles, acoustic decoys, guided artillery munitions and aircraft seat launch systems. There is no alternative to thermal batteries in military applications where requirements such as wide operating temperature range, long shelf life, maintenance-free during shelf life, fast triggering, non-self-depletion, high reliability, resistance to harsh environmental conditions and high energy density must be met simultaneously.
TÜBİTAK SAGE, Turkey's sole supplier of thermal batteries, started thermal battery technology development activities in 2002 in order to reduce foreign dependency in national projects. The thermal battery technology was developed entirely using domestic resources, and thermal battery design, production and testing capabilities were acquired.
TÜBİTAK SAGE has so far designed and produced a large number of thermal cells with different technical specifications, and the products have been qualified in accordance with international military standards. With the thermal cells developed by TÜBİTAK SAGE, the Turkish defense industry no longer depends on foreign sources for thermal cells. In addition to domestic deliveries, TÜBİTAK SAGE exports thermal batteries to many different countries, and thermal batteries have become an important export item in the Turkish defense industry.
Design
Thermal battery designs are carried out using indigenous computer software developed within TÜBİTAK SAGE. With the simulation programs developed, thermal battery performance is modeled in a computer environment and the design parameters that meet the requirements are determined.
Design options are analyzed in detail to verify that the design meets customer requirements and the results are evaluated through feasibility tests.
All results obtained from the software are experimentally verified before the design is finalized. In this context, with the test systems developed by our Institute, the sub-components that make up the thermal battery are tested at high temperature and pressure values, which are the real operating conditions they will be exposed to. As a result of modeling, simulation and test studies, the most suitable thermal battery design is determined according to power, geometry, weight, size, functionality, thermal efficiency and safety criteria.
With the possibilities provided by unique design software and test systems, thermal battery solutions needed for different applications are realized in the most accurate and fastest way.
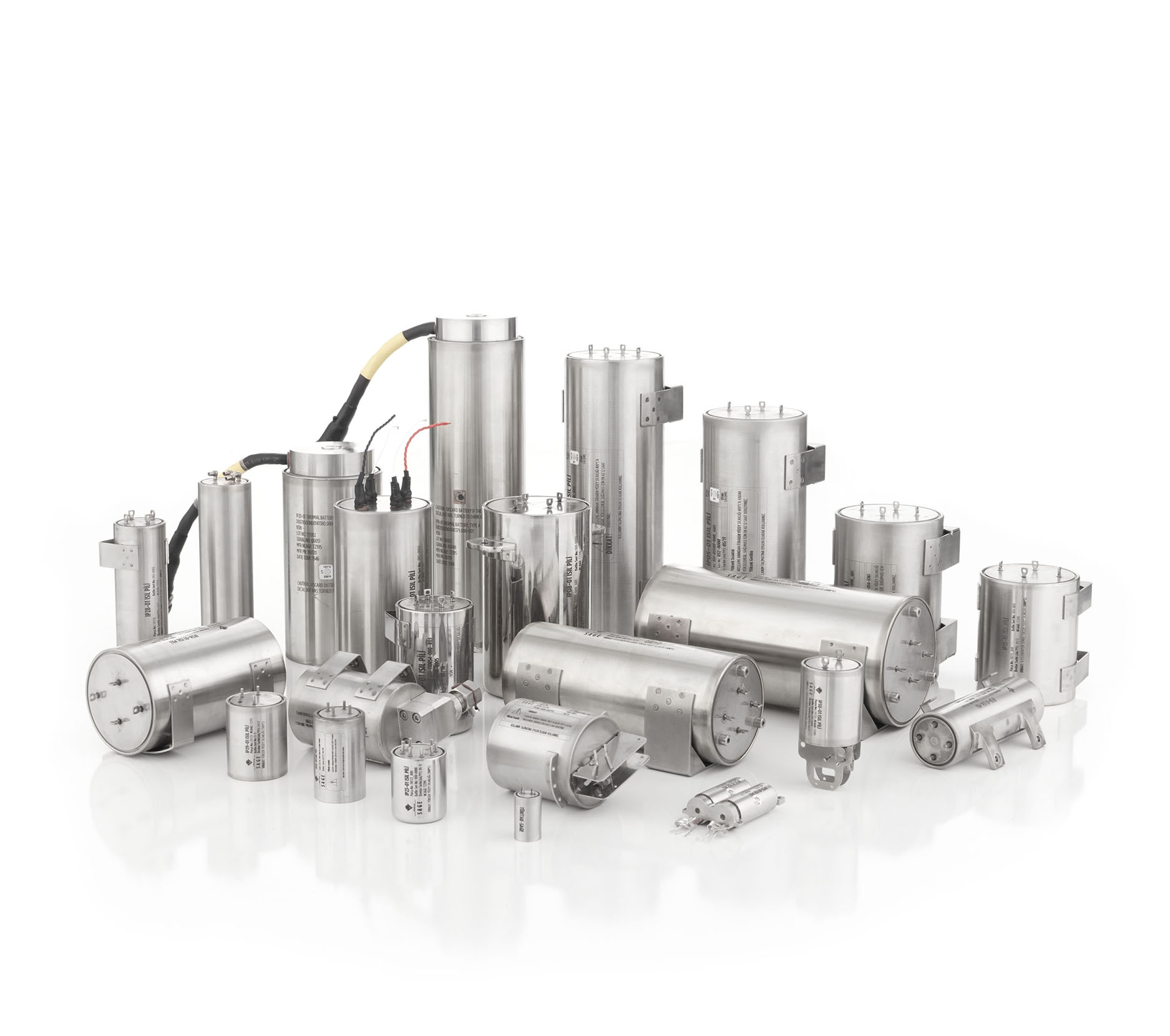
Thermal Battery Capabilities
Main Uses of Thermal Batteries
Thermal batteries are widely used as the main power source in many fields:
Missiles
Guidance Kits
Acoustic deceptive/distractions
Fuzes
Guided artillery munitions
Aircraft seat ejection systems
Advantages of Thermal Batteries
Long shelf life
> 20 years
Maintenance free
Fast triggering
< 500 ms
Alternative triggering methods
Electrical ignition, mechanical ignition, inertial ignition
Self-exhaustion
High energy density
Simultaneous multiple powering
Wide operating temperature range
-54˚C / +71˚C
Resistance to harsh environmental conditions
Thermal batteries are resistant to high levels of vibration, shock, acceleration, high and low pressure levels, high humidity, etc. during storage and operation.
High reliability
> %99.95
Special design
Thermal batteries are designed in line with the requirements of the system in which they will be used.
We Grew Stronger
In order to prevent problems such as foreign dependency, special permission, protection of confidentiality and high unit cost in the procurement of thermal batteries, which are used as the main power source in guided munitions projects carried out with national resources, and to eliminate these problems in future munitions development projects, thermal battery design, production and testing capabilities have been acquired by using entirely domestic resources; thermal battery technology, which few countries possess, has been put into the service of the Turkish defence industry by TÜBİTAK SAGE.
Production
Advanced Technology in Production
Advanced technologies are used at every stage of thermal battery production to ensure the highest level of product quality.
With the production automation systems designed by our Institute, product quality has been increased and high production capacity has been achieved. With the use of automation systems in thermal battery production, the reliability of the production line has been increased by eliminating the risks that may arise from the human factor.
Aiming for high quality and reliability in thermal battery production, TÜBİTAK SAGE has established its own glass-metal sealing infrastructure for glass-metal sealing technology, which provides thermal batteries with the advantages of long shelf life and resistance to harsh conditions.
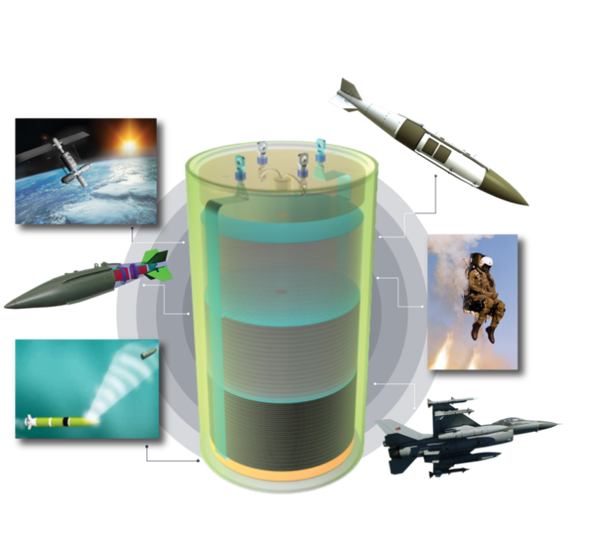
Testing
Validation Tests
In our Institute, the functional and non-functional environmental condition tests listed below are successfully applied in infrastructures with quality standardization in accordance with MIL-STD-810, MIL-STD-167-1 and AOP-34 standards:
- Electrical performance test
- Transport vibration
- Functional vibration
- Acceleration
- Electrostatic discharge
- Mechanical shock
- High and low temperature storage, cycling and operation tests
- Temperature shock
- Humidity test
- Electromagnetic environment
- Low pressure (altitude) tests
Quality Control Tests
During the thermal battery production process, a total of 215 physical-chemical quality control tests are carried out at 43 inspection points from raw material entry to intermediate product production and final product inspections. With the quality system implemented, product features are perfected and production costs are reduced.